Waste recycling pyrolysis plant
Waste recycling pyrolysis plant is mainly disposal of waste tire, waste plastic,waste rubber to fuel oil, carbon, the oil yield is about 40%-90%( depends on waste material like tire,plastic).
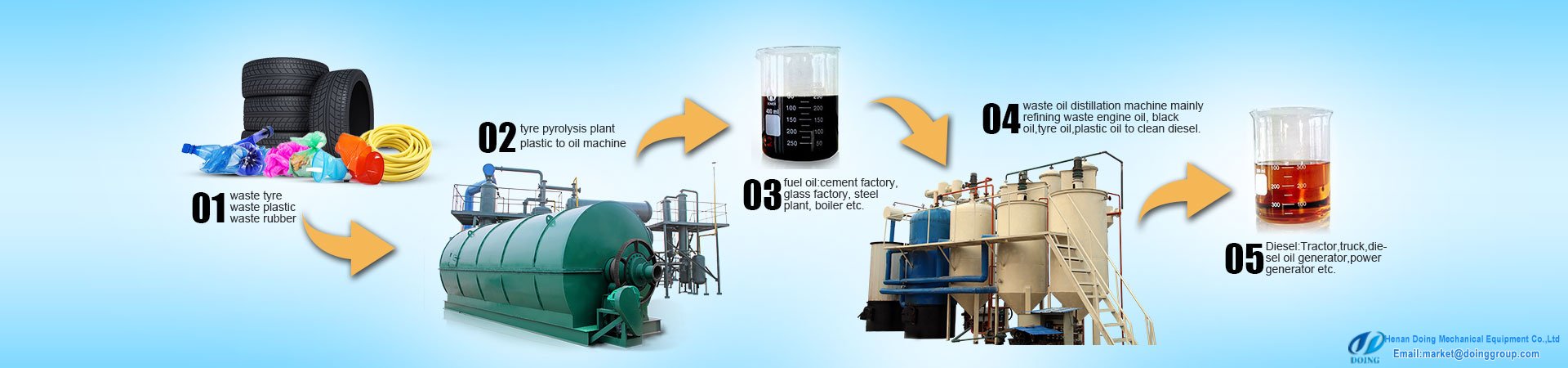
Waste recycling pyrolysis plant
Pyrolysis process of Recycling Pyrolysis Plant:
First: with 60 ton hydraulic pressure, waste tire/ plastic can be pushed to the reactor.
Second: Oil gas will be generated in the reactor after burning for 2-3hours and then go into the catalyst chamber to get purified.
Third: The purified oil gas rise up and go into the condenser pipe for first condensing. The oil gas liquefied here and flow into the oil-water separator.
Fourth: 70% of heavy oil will be collected the oil tank. The rest oil gas will go into the horizontal condenser to be condensed for the second time. 30% light oil can be separated here.
Fifth: Little remaining oil gas will come to the tail gas recycling device to be condensed for the last time. Here we can get 20-30kg oil to ensure all the oil gas liquefied.
Finally: The exhaust can be recycled as fuel resource to the burning furnace, creating a situation: burning coal for earlier stage and exhaust during later period.
Waste recycling pyrolysis plant features:
As we all know, the quality of reactor directly determines that of whole equipments. Durability can be guaranteed by the following distinctive design.
• No requitements for raw material with compound feeding ports.
• Decompress automatically with safety valve.
• Adopt I-beam steel for the base to make it strong enough.
• Special insulation makes good heat preservation and thus energy-saving.
• Made with Q245R boiler plate and welded automatically to obtain durability.
• Easy to feeding and slagging with built-in spiral plate.
• A special anti-blocking device to eliminate potential security risk.
• Easy to clean and maintain with standard gear screwed on reactor instead of welding.
• Keep stable after long time heating as supported by roller at exact place.
• Expanding oil outlet to distribute pressure and thus durable.
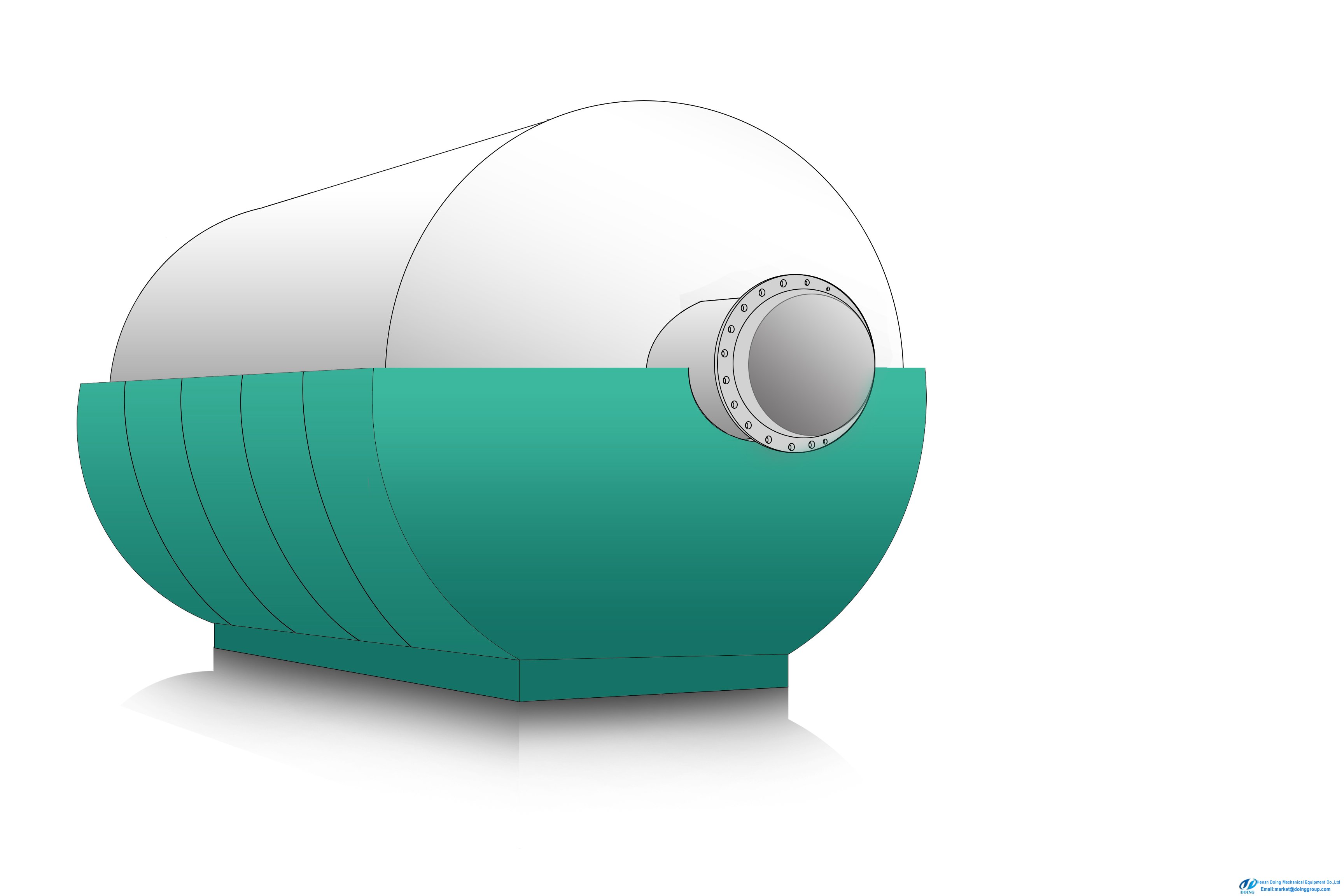
Waste tire disposal pyrolysis reactor
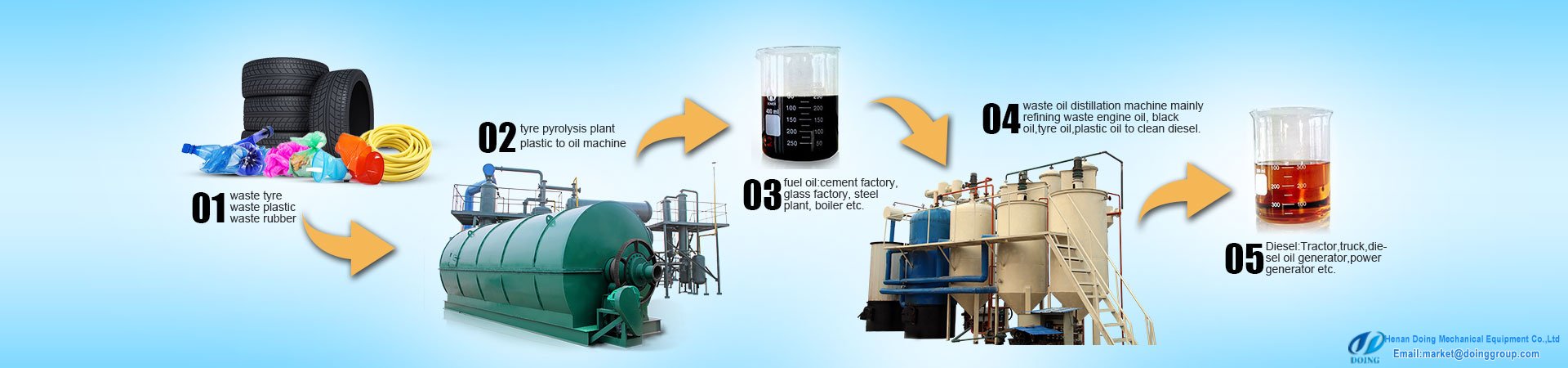
Waste recycling pyrolysis plant
Pyrolysis process of Recycling Pyrolysis Plant:
First: with 60 ton hydraulic pressure, waste tire/ plastic can be pushed to the reactor.
Second: Oil gas will be generated in the reactor after burning for 2-3hours and then go into the catalyst chamber to get purified.
Third: The purified oil gas rise up and go into the condenser pipe for first condensing. The oil gas liquefied here and flow into the oil-water separator.
Fourth: 70% of heavy oil will be collected the oil tank. The rest oil gas will go into the horizontal condenser to be condensed for the second time. 30% light oil can be separated here.
Fifth: Little remaining oil gas will come to the tail gas recycling device to be condensed for the last time. Here we can get 20-30kg oil to ensure all the oil gas liquefied.
Finally: The exhaust can be recycled as fuel resource to the burning furnace, creating a situation: burning coal for earlier stage and exhaust during later period.
Waste recycling pyrolysis plant features:
As we all know, the quality of reactor directly determines that of whole equipments. Durability can be guaranteed by the following distinctive design.
• No requitements for raw material with compound feeding ports.
• Decompress automatically with safety valve.
• Adopt I-beam steel for the base to make it strong enough.
• Special insulation makes good heat preservation and thus energy-saving.
• Made with Q245R boiler plate and welded automatically to obtain durability.
• Easy to feeding and slagging with built-in spiral plate.
• A special anti-blocking device to eliminate potential security risk.
• Easy to clean and maintain with standard gear screwed on reactor instead of welding.
• Keep stable after long time heating as supported by roller at exact place.
• Expanding oil outlet to distribute pressure and thus durable.
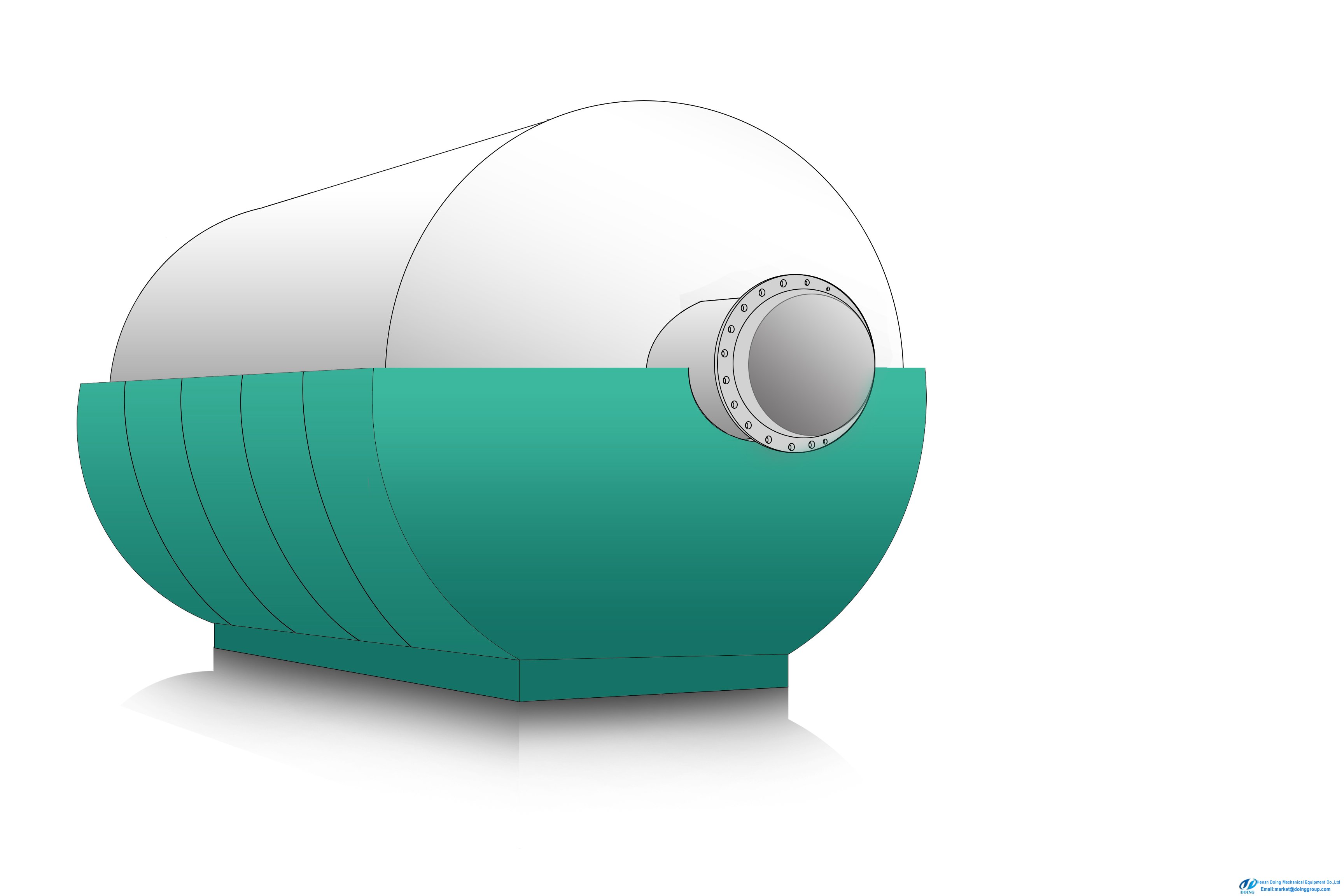
Waste tire disposal pyrolysis reactor